The application of high-tech technologies such as contemporary digital technology and computer network technology to printing machinery has undergone major changes and qualitative leaps, and has achieved a high degree of automation, informatization and intelligence. The development of printing machinery technology presents the following major trends:
Web-based printing workflow has started
The networked printing workflow is the process of promoting integrated production through solutions from several suppliers. This working method uses an open structure, networked and automated equipment, through open standard intelligent integration, using industry standards JDF (Job Definition Format) and PDF (Portable Document Format) to achieve seamless flow of information exchange, And intelligently through various systems, so as to achieve from the desktop design to the printing workshop, so that all the design information of the printed matter is transferred from the publishing house, advertising company or production center across the time, space and region to the direct platemaking machine, printing machine and post-press through the network device. In order to realize the networked printing workflow, a server, IneTone network interface, IneTone front-end software, and IneTone network interface software are also required to realize the remote transmission of jobs, samples, and samples on the Internet. Creo, headquartered in Canada, and Xerox Corporation of the United States have already joined forces and successfully launched an experimental prototype controlled online. This technology integrates the workflow of the entire printing process resources, which greatly shortens the publishing cycle. It is expected that the market will soon form in the press and publishing industry, and form a new round of network system design import peak. At the China International All-India Exhibition in 2003, Mr. Garron Helman, President of Creo Asia Pacific, introduced the products that Creo unveiled at the All-India Exhibition, and also described its future marketing initiatives, in addition to equipment In addition to products, it will focus on promoting the development of digital media, printing value, and network printing. Creo takes digital media, printing value, and network printing as its future product growth points and market growth points. It is expected that its sales revenue will reach 1 billion yuan in 2007.
CTP technology represents the development direction of printing equipment
The CTP technology includes three concepts, namely computer-to-paper, computer-to-plate, and computer-to-press. Western developed countries have successively mass produced direct plate-making machines, direct proofers, digital printing machines, and inkjet printing machines developed by CTP technology. Major suppliers of direct plate-making machines such as Creo, Sai Angel, Agfa, and Screen have proposed a variety of direct plate-making solutions, including thermal direct plate-making and photosensitive direct plate-making. The fastest direct plate-making machine in the world, the plate-making speed of the folio plate reaches 170 sheets / hour, and the four-sheet platemaking reaches 350 sheets / hour. There are many types of plate materials for direct plate-making machines, including silver salt plates, photopolymer plates, photosensitive resin plates (for flexographic printing), polyester plates, PS plates, thermal ablation plates, etc. The emergence of the direct plate-making machine makes the traditional photographic and plate-making equipment—laser imagesetter, camera, plate-making machine and other equipment face strong market competition. Some experts predict that the laser image-setting surface will withdraw from the European and American markets by 2010. There are also various ways of digital printing presses, such as in-mechanical version digital printing presses, offset digital printing dual-purpose machines, "no version" digital printing presses, inkjet printing presses, integrated machines, etc. Digital printing presses now have an industrial trend, breaking the dominance of offset printing methods. Among them, Heidelberg D146 is impacting fast printing with mechanical plate printing presses and Israeli plateless digital printing presses and ideal all-in-one printers, copiers. The market has already threatened the office printing market and photo-engraving equipment represented by small offset printing presses; the other wing of digital printing presses-Heidelberg D174 and Manroland digital printing presses, can achieve both traditional offset printing and direct imaging printing This large-format printing will also pose a threat to the traditional offset printing market; large-format inkjet printers can produce street and body advertisements and wallpapers, thus posing a threat to paper gravure printing machines and screen printing machines. Digital printing presses are currently suitable for "short version" printing or personalized printing, and they cannot pose a threat to newspapers, books, and packaging printing in large quantities. With the rapid development of the market economy, "short version" and personalized prints will increase rapidly. According to statistics, there were more than 3,000 printing plants using CTP technology in the United States in 2003. The rapid popularization of CTP technology equipment is a foregone conclusion.
Market expansion of green printing methods
Flexographic printing is a relief printing method. Its production was developed after solving photosensitive resin plate and plate-making equipment, water-based ink, anilox roller and its engraving equipment. The flexographic printing machine is an automatic production line mainly based on flexographic printing, integrating multiple printing methods and auxiliary functions. Its successful trial production mainly depends on the combined configuration of flexographic printing and glaze coating, screen printing, vertical and horizontal die cutting, and bronzing, which can complete the production requirements of specific trademarks, folding cartons, and flexible packaging products at one time. This kind of equipment has no water-ink balance problem, the ink path is relatively simple, quantitative ink transfer, water-based ink meets the requirements of green environmental protection.
Taking the changing trend of packaging and printing methods in the world as an example, the share of flexographic printing in the packaging field will further increase. Foreign flexographic printing has expanded into the fields of news publishing and flexible packaging, especially in Europe and America. At present, 40% of the packaging printing in the European packaging and printing market is offset printing, and flexographic printing is also developing rapidly, accounting for 32%. It is reported that there are more than 400 flexographic printing companies in certain countries in the European Union. A large number of countries are 950 in Italy, 800 in Germany, 650 in the UK, 500 in France, and 350 in Northern Europe. In recent years, flexographic printing has also become a major focus of the North American packaging paper printing industry. According to the statistics of the North American Flexo Printing Technology Association, more than 6,000 flexographic printing companies in North America had a total printing output of more than 85 billion US dollars in 2003, an increase of 5%, and flexo printing accounted for 74% of the North American packaging printing market. It accounts for 24% of the world's printing and publishing market, covering the market areas including flexible film packaging, paper bag multilayer packaging bags, labels, corrugated paper pre-printing, folding cartons, envelopes and so on. It is estimated that by 2005, flexographic printing will exceed offset printing in the world, and the proportion in the packaging field will reach 39%, while gravure printing will account for 15%, and other printing methods will account for 10%.
In addition to flexible flexographic printing, some foreign companies currently use water-based environmentally friendly inks and anilox rollers for quantitative ink transfer on offset presses, which is also a promising combination of environmental protection. Other green printing machinery and equipment include water-based UV printing device, water-based UV glazing machine, dry laminating machine, water-based laminating machine, etc. The technical problems related to these products have been solved.
Printing machinery automation level improved
The level of printing machinery automation is mainly manifested in four aspects: mechanization, stand-alone automation, automation of auxiliary operations and automation of the production process of printed products. In the printing process, the mechanized manual operation process is mainly after printing. Many printing companies' book binding (folding, matching, gluing), newspaper distribution (insert, several pages, bundling) are still manual operations; Before printing, there are companies using manual puzzles. These operations can be completely solved with book binding equipment, automatic newspaper publishing equipment automatic typesetting system. The low level of stand-alone automation in the printing process is mainly reflected in pre-press and post-press, such as printing machine, copying machine, paper cutter, bronzing machine, die-cutting and creasing machine, etc. Now these equipments have been replaced with new products, such as German paper cutting machines, Swiss boster die-cutting bronzing machines and automatic plate-making machines and other high-end equipments, which can greatly improve the level of stand-alone automation in the printing process. Auxiliary operation automation of printing machinery, mainly represented by high-end offset presses, in addition to frequency conversion, PLC, CP window, CPU, CPC, automatic registration, ink-water balance and nonlinear tracking, automatic paper conversion presetting , Auto-piercing, auto-rubbing, auto-changing, auto-loading, auto-turning double-sided printing, rewinding function, single sheet cutting function and other mature technologies. This high-end offset press mainly comes from foreign companies such as Heidelberg, Manroland, KBA, Komori, Mitsubishi, and Gauss. The automation of the production process of printed products includes two aspects: one is the transmission of printed information, that is, the digital workflow, which is solved by the corresponding interface of standardization, software and hardware; the other is the connection of the equipment used in the printing process, as already solved in the world Books and periodicals bookbinding once book-forming equipment.
There are also some equipments that have already realized the configuration of multiple functions, such as the multiple printing methods of flexographic printing machines and the combination of cutting, die-cutting and bronzing; the printing, punching, marking, rewinding and glazing of form printing machines , Carbon coating, vertical and horizontal entanglement lines, format conversion and other functional combinations; the paper cutter also realizes the automation of paper loading, page breaking, fractionation, paper cutting, conveying, paper lowering, and die cutting. In recent years, in order to protect independent intellectual property rights and corporate interests, anti-counterfeiting printing technology has been widely adopted in the printing of printed matter or securities. Anti-counterfeiting technology in addition to anti-counterfeiting ink and anti-counterfeiting watermark paper, there are anti-counterfeiting measures such as holographic bronzing stamping anti-counterfeiting, Moire stripe screen printing anti-counterfeiting, and various printing process combination anti-counterfeiting. These requirements are generally connected to the equipment for printing, which greatly improves work efficiency.
Increased working accuracy of printing machinery products
With the development of CNC technology, the working precision of printing machinery products and the machining precision of parts have been greatly improved. For example, after the assembly of plate cylinders, rubber cylinders, and impression cylinders produced by foreign companies, the parallelism and radial runout have reached 0.001-0.003 mm, and the accuracy of overprinting between units has reached 0.01 mm. Another example is the recently launched satellite-type small five-color lithographic printing machine abroad, so that there is no paper handover between the printing color groups, and the paper transfer error is zero. Other products use double-diameter impression cylinders and triple-diameter impression cylinders, which reduces the paper transfer of four-color machines from 12 times to 4 times from the paper between the units, and also improves the printing quality. In addition, the ink roller cooling technology, alcohol dampening plate, cylinder dynamic balance, long and short ink path switching function, double-sided printing function, fast paper setting function, etc. have all further improved the working accuracy of the printing press.
For Trick Dice we have 7/11 dice and loaded dice. Our 7/11 dice is 18MM, they look like regular dice, but they roll seven or eleven on every single throw. 7/11 Trick Dice come in pairs that feature one die that has six dots on all sides and a second die that has three sixes and three twos on the sides.
For loaded dice we put in metal piece, to make dice tend to stop at appointed side. Custom loaded dice is welcomed.
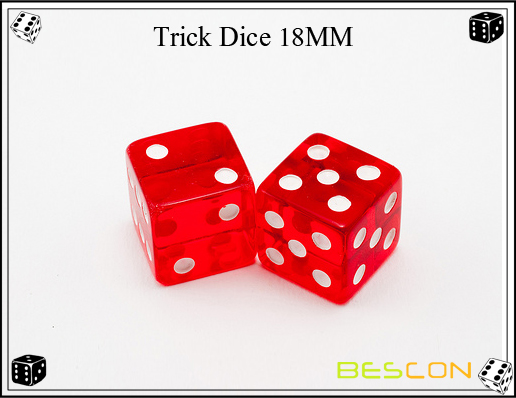
Trick Dice
Directly Magic Trick Dice,Trick Bomb Dice,Small Magic Trick Dice,Fashion Trick Dice
BESCON INDUSTRIAL CO., LIMITED , http://www.besconcn.com