The use of the polyurethane waterproof material is quite convenient, and it can be cured at room temperature after being mixed and coated at room temperature to obtain a waterproof layer with seamlessness, rubber elasticity and good performance. And easy to repair after damage. It is generally used as flooring material, track and field track materials, racetracks, park floor materials, and thermal insulation window frames.
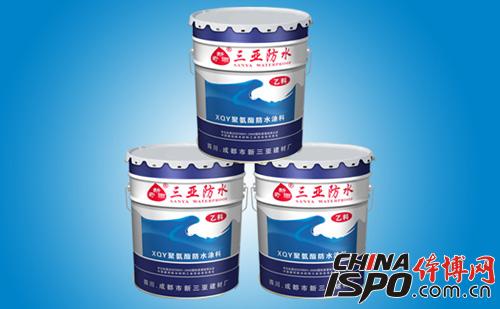
Construction preparation:
1, the main material:
Part A (prepolymer)
Part B (cured body)
2, construction tools:
Name Use Name Use
Electric mixer mixes A and B materials with a paint brush
Mixing bucket mixing A, B material with rolling brush brush primer
Small paint bucket mix with a small trowel to repair the base layer
Plastic Scraper Scrape Mixer Cleans Base Layer with Oiler Blade
Tin scraper scrapes mixture on a complex area to clean the base layer
Rubber Scrape Scrape Mixture with 50kg Scale Weighing
Process flow:
Base Surface Treatment→Polyurethane Primer→Local Enhancement→Scrape Polyurethane Coating One, Two, Three Times→Surface Protection or Modification
Grassroots requirements and processing:
1. The waterproof base should be applied with 1:3 cement mortar to make a 1/50 flooding slope according to the design requirements. The surface should be smoothed and calendered, and there should be no defects such as unevenness, looseness, sanding and ashing. Drain outlets or floor drains should be lower than the entire waterproof layer in order to remove accumulated water. The pipe part with casing should be more than 20mm above the surface of the base layer. The corners of the yin and yang should be made with small round corners with a radius of 10mm for coating construction.
2. All fittings, sanitary equipment, floor drains, or drain outlets must be securely installed with tight joints and rounded surfaces without any loosening.
3. During construction, when the traditional polyurethane waterproof coating is applied, the waterproof base layer should be basically in a dry state, and the moisture content is less than 9%. The simple measurement method is to cover the rubber plate with an area of ​​1m2 and a thickness of 1.5-2.0mm. On the base level, it is allowed to stand for 2 to 3 hours. If there is no watermark on the surface of the covered base layer, the rubber plate close to the base layer has no condensation watermark. According to experience, the water content has been less than 9%, which meets the construction requirements.
4. Before the construction, remove the foreign materials such as protrusions, mortar, etc. on the surface of the base with a blade and a broom, and thoroughly clean the dust and debris. For yin and yang angles, pipe roots, floor drains, and drains, etc., they should be carefully cleaned. If oil, rust, etc. are found, clean them thoroughly with wire brushes, sandpaper, and organic solvents.
Construction requirements
1, coating primer: This process is equivalent to the traditional asphalt waterproof construction brushing cold base oil, its purpose is to cut off the primary moisture, prevent the waterproof coating from the drum off; reinforcement base layer, improve the adhesion strength of the coating and the base layer to prevent The coating has defects such as pinholes. It is recommended to use polyurethane primer as the base layer.
Polyurethane primer preparation: The polyurethane A material, the material ratio of 1:2 to 3 (weight ratio) with (the other coating according to the product specifications required proportions). When the material is thicker, it can be diluted with a special diluent, and must not be diluted with acidic or oily diluents so as not to affect the quality of the original product. In the preparation, the first material should be diluted and stirred for 2-3 minutes. If no dilution is needed, it can be directly distributed and agitated for 5 to 10 minutes with the group A and B. The stirrer can be lifted, and it can be seen that the uniform liquid slowly slides from the container. At the same time, it should be noted that the open material should be tightly closed immediately to avoid solidification and scrapping. The mix should be used according to the actual amount. (Note: When mixing 991 construction materials, mix A material into the material to stir it, contrary to Type 911 and Type 851)
2, local enhancement: expansion joints, control joints, yin and yang angle, pipe joints, etc., can be reinforced by a layer of reinforced cloth, solidified and then the overall waterproof construction.
3, the first pass of coating construction: After the primer is basically dried and solidified, evenly smear a layer of paint with a plastic or rubber scraper. When the scraping is required, it must be uniform, not too thick or too thin, and the thickness of the scratching is generally 0.8. Mm is appropriate. When starting to scratch, the construction shall be based on the size of the construction area, shape and material, and consider the construction of road escape and smearing order.
4, the second pass of coating construction: After the first pass of the coating is basically cured, and then apply a second coating on the surface of the coating, and the coating method is the same as the first coating. In order to ensure the quality of the waterproof project, the direction of the scratch must be perpendicular to the scratching direction of the first layer. The interval of recoating time is determined by the temperature at the time of application and the degree of curing of the coating film (non-stick by hand).
5. After the second pass of the film has cured, apply the third pass of the film as described above.
6. Laying a protective layer or decorative material: When the third pass of the coating is completed and not completely cured, a small amount of clean sand (diameter not more than 2mm) may be sprinkled on the surface to increase the coating layer and will The bondability between covered cement mortar. When the coating film is completely cured and the inspection and acceptance pass, you can wipe the protective layer of cement mortar or paste the tile, mosaic and other finishes.
7, two cloth three coating construction process: This process is not currently used in the market, the operation method of this process is: in accordance with the above description for the grassroots and other processing is the same, after brushing the first pass, will The glass fiber grid cloth is evenly laid on the top and adhered firmly by the adhesive force of the polyurethane. After the first time drying, the same method is performed for the second time. After all the drying is completed, the polyurethane waterproofing is finally applied according to the above requirements. coating. The construction methods for the bathroom, kitchen and roof are the same. It should be noted that the glass fiber grid needs to be flat when paving. Since the space of the toilet is relatively small, it should be dealt with before the grid cloth is applied. Other requirements are consistent with the traditional polyurethane construction process requirements.
Precautions
1. When the paint viscosity is too large to apply the scratch coating, a small amount of special thinner may be added to reduce the viscosity, and the amount added must not be greater than 10% of the material. (Note: If you need to dilute polyurethane, you must use the company's supporting thinner. If you buy the market xylene, gasoline and other thinners, resulting in quality problems, the company is not responsible.)
2. Blowholes and air bubbles: Material mixing methods and mixing time do not mix the materials evenly; the mixers with low power and high rotation speed should be used during construction. Another reason is that the grassroots processing is not clean. Before the coating is done, the base layer should be carefully cleaned. There should be no floating sand and dust. There should be no pores on the base layer. The pores in each layer of the coating should be treated according to the process requirements to prevent the destruction of the coating film. Causes leakage.
3, from the drum: the base layer from the skin, sand, cracking, not dry, so that poor adhesion of the coating; base construction should be carefully operated, conservation, until the base is dry, the first coating primer, curing, and then press the waterproof layer The construction process is brushed layer by layer.
4, coating Alice: the edge of the waterproof layer, the overlapping part of the brush at the same time, with the grassroots peeling phenomenon. The main reason is that the grass-roots floor is unclean or not dry, the head-receiving operation is not detailed, the seal is not good, the adhesion of the primer coating is not strong, etc. Therefore, the grass-roots level should be clean and dry, and the operation should be meticulous.
5, damage: coating film waterproof layer layering construction process or all the film is completed, not on the film curing on the master operating activities, or place the tool material, etc., will damage the film. Scratch. The integrity of the coating should be protected during construction.
6. Fire prevention should be taken during construction. Construction personnel should take protective measures. The construction site requires good ventilation to prevent solvent poisoning.
7. If there is a precipitation phenomenon in the work material, it should be used after stirring evenly so as not to affect the quality.
8. Both A and B materials are iron drums, flammable and toxic. They should be sealed during storage and placed in a cool, dry place with no direct sunlight.
9, the construction temperature should be above 5 °C.
Related Reading:
Comparison of Differences between Traditional Rigid Acrylic Materials, Pu Pu Materials, and Silicon Pu Stadium Materials
Http://
PU-polyurethane
Http://
STURDY AND HYGIENIC - The solid silicone surface leaves no crevices for bacteria to collect. The premium kitchen spatula is firm enough for mixing both wet and dry ingredients together. The silicone kitchen spatula set is especially suited for kitchen tasks because of its smooth edges and sturdiness.
HEAT RESISTANT -The baking turner spatula has a very high melting point which gives it the ability to stir extremely hot mixtures or remove food directly. Accident exposure to heat can permanently damage rubber or plastic utensils, but the heat resistant silicone spatulas won't be.
UNIBODY DESIGN AND MUTI-USAGE -A one piece design allows for increased stability and durability. The chef's hygienic spatula can be used as cake spatula, batter scraper, jar spatula, egg spatula, fish spatula and BBQ spatula.
NON-STICK - Kitchen Silicone spatulas are safe for non-stick pots and pans, and the utensils won't transfer any unpleasant tastes to the food it contacts. Silicone spatulas won't rust or discolor. The handles of the silicone spatulas are made of a special kind of silicone, which is used for high temperature situations.
DISHWASHER SAFE - Silicone Spatula can be cleaned in the same way as regular cooking utensils, either by hand or in the dishwasher. Do not use abrasive cleaning pads, as they can scratch the surface of silicone and should be avoided.
Silicone Spatula,Silicone Brush,Kitchen Silicone Spatula,Silicone Pastry Brush
YANGJIANG TOALLWIN TRADING CO., LTD , https://www.kitchenknife.de